PROCESSING APPLICATION
Hold tight! We’re comparing your resume to the job requirements…
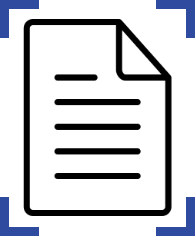
ARE YOU SURE YOU WANT TO APPLY TO THIS JOB?
Based on your Resume, it doesn't look like you meet the requirements from the employer. You can still apply if you think you’re a fit.
Job Requirements of Plastics Manufacturing - Engineering Manager - Dover, NH:
-
Employment Type:
Full-Time
-
Location:
Dover, NH (Onsite)
Do you meet the requirements for this job?
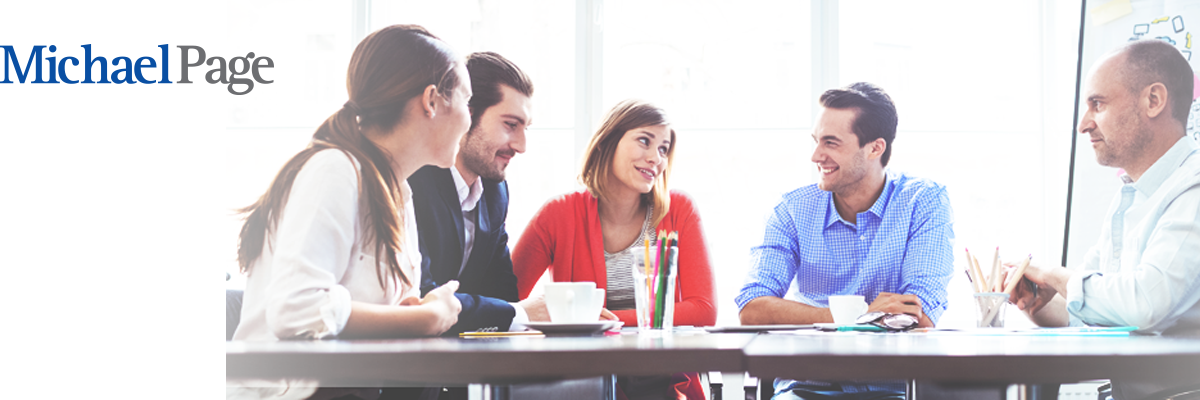
Plastics Manufacturing - Engineering Manager - Dover, NH
The Engineering Manager leads manufacturing operations, overseeing process control and product development from customer quotes through production launch. They guide engineering teams in troubleshooting, process improvements, and material selection while managing new initiatives. This hands-on leader champions workplace safety and operational excellence through effective team mentoring and continuous improvement practices.
Client Details
My client is a trusted manufacturing partner, known for engineering expertise and flexible solutions in sealing and molded components. With a commitment to long-term partnerships and respectful collaboration, they deliver top-tier service that drives client success.
Description
Responsibilities:
- Adhere to and enforce all safety and company policies, reporting violations and hazards to superiors or the Safety Committee.
- Promote safe practices on the shop floor and actively report safety concerns to the committee.
- Serve as the process owner for new process development in injection, compression, and transfer molding.
- Oversee design, planning, and procurement of new tooling, coordinating reviews to align with customer expectations.
- Lead new product reviews and oversee their transition to the production floor.
- Plan First Article Runs and support engineering production startups, driving seamless production transfers.
- Coordinate daily engineering team activities across departments to ensure alignment and productivity.
- Develop, document, and lead process improvement efforts to enhance safety, quality, and cycle times.
- Collaborate with suppliers and procurement to specify new materials and identify potential improvements.
- Provide training and coaching for production and engineering personnel, reinforcing best practices.
Profile
Ideal Candidate:
- Proven leadership skills with a focus on achieving results through team collaboration.
- Strategic planner with the ability to forecast and set goals 1-2 years ahead.
- Skilled at managing multiple tasks and prioritizing effectively in a fast-paced environment.
- Creative problem-solver, with innovative, out-of-the-box thinking.
- Strong customer focus and conscientious approach to delivering quality results.
- Team-oriented with excellent interpersonal skills to create consensus and maintain productive relationships across all levels.
- Decisive decision-making abilities and strong organizational skills.
- Technical expertise in manufacturing techniques, Kaizen, process improvement, and materials management.
- Proficient in project management, lean principles, and software tools, including Microsoft Office, SolidWorks, and MRP systems
Job Offer
What's To Offer:
- Attractive compensation with room for financial advancement.
- Comprehensive health and wellness coverage.
- Growth-focused career development and mentorship opportunities.
- Dynamic and collaborative workplace culture.
- Exposure to advanced technologies and ongoing learning support.
- Engagement in impactful and forward-thinking projects.
MPI does not discriminate on the basis of race, color, religion, sex, sexual orientation, gender identity or expression, national origin, age, disability, veteran status, marital status, or based on an individual's status in any group or class protected by applicable federal, state or local law. MPI encourages applications from minorities, women, the disabled, protected veterans and all other qualified applicants.